Chimney Crack Inspection: How to Detect, Prevent, and Repair Chimney Damage Safely
Key Takeaways
Chimney crack analysis stands essential for safety reasons and operational workflow requirements. Regular exhaustive checks prevent both water damage and smoke leaks as well as fire dangers that could arise because of hidden cracks.
The combination of severe weather conditions regularly produces the primary cause of chimney deterioration through various cracks. Masonry deterioration occurs from freeze-thaw effects during stormy or temperature-sensitive periods so building inspectors need to perform urgent checks of affected structures because of structural safety risks.
Little appearing fractures close to the chimney base have the potential to expand into substantial building problems. The depth measurement of cracks revealed to professional inspectors during structural evaluations enables them to locate concealed problems that need specific maintenance remedies.
Preventative maintenance reduces costly repairs. Your chimney will last longer through regular annual inspections combined with proper cleaning methods and waterproof materials and strong liners.
Specialized professionals both inspect the entire chimney system and perform safe repair work on it. Detailed chimney maintenance only succeeds when expert professionals from organizations such as CSIA or NFPA maintain the system’s safety for continuous operation.
Negligence allows minor initial cracks in chimneys to become serious difficulty. Minor chimney system cracks produce various safety threats which negatively affect both home operational efficiency and safety measures. Chimney system safety arises directly from scheduled examinations for detecting cracks.
Chimney crack evaluation identifies potential hidden problems which may develop into severe problems in the future. The text explores why chimney cracks occur before describing how to detect them along with appropriate repair steps. Chimney inspections periodically will preserve both operational excellence and residential security.
Importance Of Chimney Crack Inspection
Home protection together with increased chimney structural life expectancy result from regular chimney crack inspections. The seemingly minor cracks that run along a masonry structure generally indicate deep structural problems requiring appropriate maintenance.
Reasons To Inspect Chimney Cracks:
The entrance of water through damaged chimney mortar causes crumbling walls and weakened masonry that allows mold development. Using crack waterproofing stops water from penetrating while it reduces expenses connected to costly repairs.
Structural safety evaluations identify essential points that put the chimney in danger of structural collapse. An improper chimney inspection enhances the likelihood of both damaged homes and fires.
Chimney structures deteriorate steeply after freezing temperatures combined with melting and weather damage. Early detection of problems shields both the building structure from damage and avoids the need for home maintenance expenses.
Potential Problems From Overlooked Cracks:
Open chimney cracks permit damaging gases together with vapor to seep into household areas. Proper attention to crack repair procedures ensures the safety of residential chimney vents.
High heat damages the structure because cracks allow direct transmission of dangerous heat to combustible building elements. Professional evaluations including depth analysis of structural cracks perform an important role in reducing the threat of chimney fires.
Proficient experts in crack stability determine the condition of expanding and stable cracks. This guides necessary repairs.
The condition of masonry structures becomes worse when cracks occur and leads to performance deterioration. Masonry professionals thoroughly examine fractures that are visible on exterior walls along with those hiding inside the building.
Inspection professionals use Crack Progress Detection to detect deteriorating conditions that need immediate proper repairs for the damaged areas.
Any chimney with untreated cracks will result in both safety hazards and higher costs. The prevention of extensive structural damage requires regular inspections that need to happen before heaters start operating for the winter season. Two reputable organizations provide guidelines about this matter: Chimney Safety Institute of America (CSIA) along with National Fire Protection Association (NFPA).
Common Causes Of Chimney Cracks
The development of chimney cracks originates from multiple factors that simultaneously endanger both security systems and structural foundation of buildings. Earliest identification of these causes through knowledgeable awareness helps prevent conditions from worsening into major issues.
Weather Conditions
The combination of polar and scorching weather conditions creates fractures in chimneys. Wet masonry absorbs water from rain until exposed temperatures create ice which expands inside the materials. The combination of freezing temperatures with thawing results in weather-induced cracks. The repeated phenomenon separates components of the structure until water begins to seep through created openings.
Heat also impacts chimneys. Masonry bricks expand under high temperatures because they generate stress that results in cracking. Harmful expansion exists at the starting points of hairline cracks which grow worse if no crack sealing applications are made.
Strong winds together with stormy conditions have negative effects on masonry chimney integrity. Strong winds break damaged bricks and storm water permeates into the mortar joints thus making the material more likely to spread cracks. Schedule a stability check of cracks ahead of expected harsh weather seasons to reduce damage.
A detailed overview of chimney weather preparedness exists in the materials provided by the Chimney Safety Institute of America (CSIA).
Structural Issues
Age-related houses commonly develop chimney cracks because of their structural conditions. Foundations that shift base their load on the chimney which causes diagonal or vertical crevices to appear on its structure. Assessing structural cracks helps establish whether instant repair of these cracks is necessary.
Poor construction also impacts durability. Faulty installations of fireplaces along with weak mortar joints create serious risks to the overall functional strength of a chimney. General use stress accelerates the formation of cracks in chimney structures.
Earthquakes along with changes in ground level create damage that affects masonry structures through cracks. Small earthquake happenings cause bricks to change their position which creates noticeable cracking. The consequence of neglecting slight cracks consists of future damage that affects the structure in a bigger way. Height measurement of these minor cracks helps determine their degree of severity.
Contact experienced professionals for full structural evaluations in case of emergence of structural concerns. Accurate guidelines for safety standards are published by the National Fire Protection Association (NFPA).
Poor Maintenance
The outcome of poor chimney maintenance leads to faster development of cracks in the structure. Brick exposure to moisture occurs when soot and dirt and creosote accumulate and deteriorate bricks and mortar through trapped moisture thus producing cracks. Continuous maintenance activities prevent the buildup of materials which thus reduces the necessity of repair work.
Rain and debris will enter the chimney when caps are missing or damaged. The presence of water creates damage to mortar joints that eventually leads to more cracks. Chimney caps must be installed or repaired for preventive purposes to avoid expensive future costs in waterproofing processes.
Regular checks discover minor complications which stop them from becoming more significant problems. Masonry deterioration can be identified at its early stage through assessments of tiny hairline cracks. The harmful effect of such cracks increases when they remain untreated before causing advanced destruction to the structure.
Traditional inspection processes that happen at regular intervals help prolong the operational lifespan of chimneys. Such proactive maintenance practices reduce expenses while sustaining a protected house environment that benefits every member of the household.
Signs Your Chimney Needs Inspection
Routine chimney checks detect developing problems to stop expensive maintenance costs. You can determine professional assessment time through the following recognition methods.
Visible Cracks
Any flaws or cracks appeared on chimney masonry or flue lining necessitate immediate professional attention.
When frost causes hairline fractures at the chimney they might continue to spread and grow into more serious fractures resulting from weather conditions.
Roomy openings between mortar joints deteriorate chimney stability and need professional inspection of the damage.
Significant cracks in your chimney structure enable the dangerous gas carbon monoxide to flow into your house.
Visible damage when left unaddressed means you will face more costly expenses in crack restoration work. A proper structural crack evaluation needs the expertise of a certified professional to guarantee complete security. To access reliable information about CSIA chimney safety standards you should refer to them.
Water Leaks
Water staining around the fireplace or on walls exists as a sign of wall fractures.
The acceptance of waterproof treatment for cracks becomes necessary whenever water penetrates into masonry structures. The presence of moisture causes bricks to deteriorate while mold accumulates as a result.
Chimney caps together with flashing need immediate repair to stop worsening water penetration.
Monitoring water leaking should be immediate since it causes structural damage to homes located in regions with high precipitation. To get additional direction refer to NFPA guidelines.
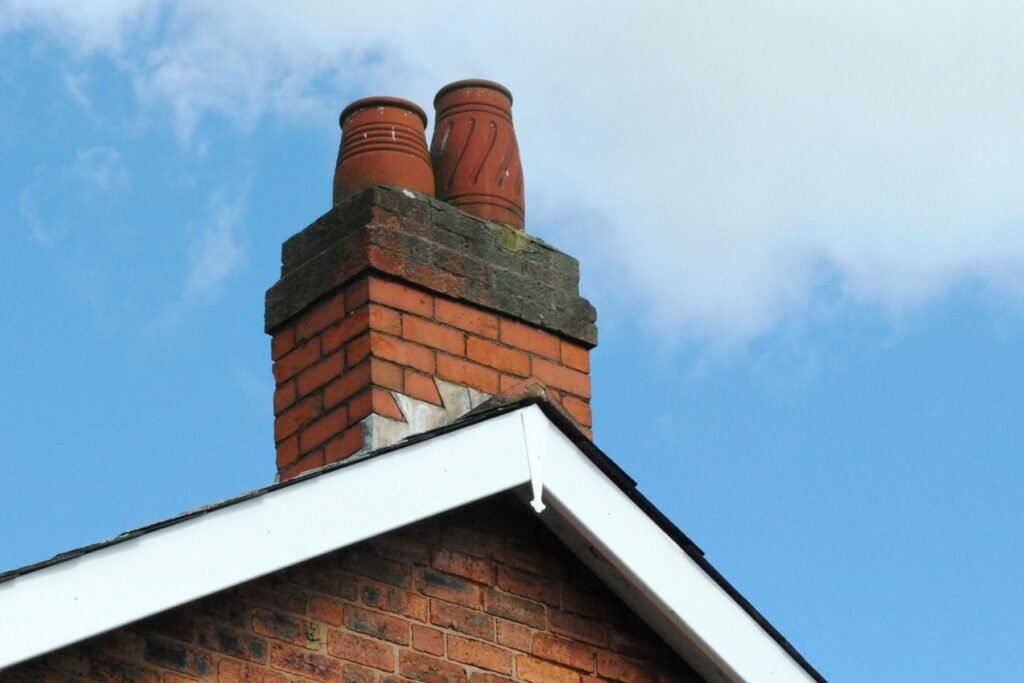
Drafting Problems
Inconsistent draft performance in chimneys indicates airflow disruption.
- Poor draft could mean crack propagation detection is needed to locate internal blockages or cracks affecting venting.
- Smoke backflow into rooms suggests a cracked liner or obstructed airflow.
Timely hairline crack assessments help maintain efficient draft and prevent smoke build-up. Address drafting issues early to ensure safe heating during colder months.
Steps In A Professional Chimney Crack Inspection
Professional chimney crack inspections are essential to uncovering hidden issues and ensuring chimney safety. Let’s break down the core steps to better understand what happens during this process.
Initial Assessment
The inspection begins with a detailed visual assessment of the chimney’s exterior and interior surfaces. We look for visible cracks, discoloration, loose masonry, or rust, which often signal weather-induced cracks or structural problems. Particular attention is paid to hairline cracks, as these might seem minor but could be early signs of crack propagation.
Chimney crowns, flue liners, and mortar joints are inspected carefully since they are the most susceptible to damage. Any signs of water leaks, draft problems, or creosote buildup are noted, as their presence typically indicates underlying issues, like the need for crack waterproofing or structural evaluations.
Neglecting these preliminary checks can lead to safety concerns or expensive repairs. That’s why this stage sets the foundation for further examination and targeted fixes, ensuring nothing is overlooked.
Use Of Specialized Equipment
Special tools make the inspection process thorough and reliable. Chimney cameras are used to get a clear view of hard-to-reach areas like the flue interior. These cameras help us identify hidden masonry crack impacts and determine crack depth analysis accurately.
Moisture meters probe for water intrusion, which points to potential cracks needing sealing or waterproofing. When assessing structural damage, laser devices are utilized for precise measurements during structural crack evaluations. Tools like calipers allow us to measure crack width and monitor stability to ensure the cracks haven’t worsened over time.
Without this specialized equipment, it’s easy to miss critical details that could compromise the chimney’s safety or efficiency. The proper use of these tools is crucial for diagnosing chimney issues precisely.
Documentation And Reporting
Comprehensive reports summarize findings and recommend corrective actions. Our team documents crack locations, types, and severity, including distinguishing between hairline cracks and deeper structural concerns. Photographs from inspections, especially using chimney cameras, provide a visual record for better understanding.
Reports include recommendations for crack repair methods, such as sealing minor cracks, waterproofing masonry to prevent water damage, or restoring compromised flue liners. Crack stability checks and crack propagation detection are thoroughly detailed to guide homeowners in addressing issues effectively.
These inspection reports not only inform but also support homeowners when seeking professional repairs. For professional guidance, refer to the Chimney Safety Institute of America (CSIA) or the National Fire Protection Association (NFPA), both of which emphasize regular chimney inspections for safety.
Repair And Maintenance Options For Chimney Cracks
Repairing chimney cracks involves addressing both minor and severe issues to maintain structural integrity and safety. Let’s explore effective options below.
Sealants And Patching
Sealants and patching provide quick solutions for minor surface damages. Hairline cracks or shallow masonry cracks often fall into this category. Applying crack-specific sealants prevents water intrusion and further deterioration, especially in cases of weather-induced cracks.
For cracks affecting waterproofing, flexible waterproof sealants work well. Masonry patching compounds, designed for high-temperature resistance, are ideal near the chimney crown or firebox area. Crack sealing needs vary based on crack depth, so thorough crack depth analysis ensures the right products are used.
While patching handles smaller cracks, consulting a professional confirms there are no underlying structural issues. The Chimney Safety Institute of America (CSIA) recommends professional evaluations to determine whether cracks impair chimney stability.
Relining The Chimney
Relining works best for damages to the chimney flue. Damaged or cracked flue liners let gases like carbon monoxide seep into homes, posing health risks. Flue relining ensures a smooth, insulated passage for safe airflow and combustion.
Several crack repair methods for liners exist. Stainless-steel liners are durable and efficient for damaged systems. Relining with cast-in-place materials provides structural crack reinforcement while sealing fractures, including those caused by freeze-thaw cycles or weather-induced cracks.
While analyzing crack propagation helps, professional expertise is necessary to select the proper liner type for specific needs. During assessments, technicians perform a structural crack evaluation to rule out advanced masonry concerns. Relining supports long-term chimney functionality, particularly in regions with extreme temperature changes.
Full Chimney Reconstruction
Severe chimney damage requires reconstruction. This includes rebuilding the chimney stack or relaying brickwork when foundational cracks compromise structural integrity. For damage caused by settling, advanced masonry crack impacts are addressed through professional engineering techniques.
Reconstruction resolves issues extending beyond crack waterproofing and sealing. During this process, experts stabilize and inspect surrounding structures for potential risks. Chimneys facing advanced crack propagation detection, particularly from neglect, often benefit from complete rebuilding.
While it might sound dramatic, reconstruction is sometimes the safest route. Regular crack stability checks keep reconstruction needs to a minimum. To ensure standards, the National Fire Protection Association (NFPA) provides guidelines on safe practices.
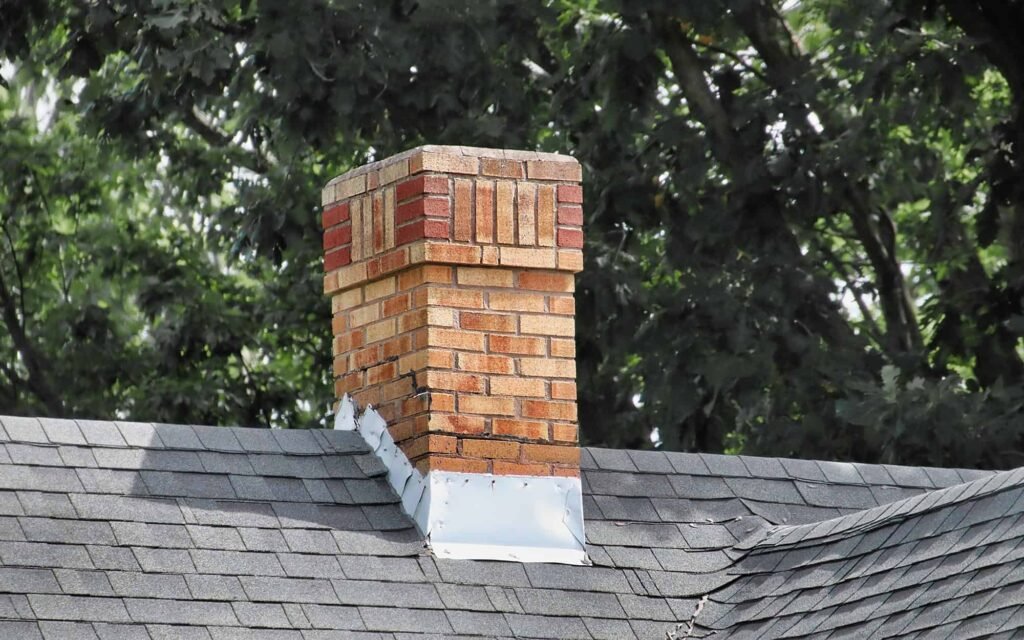
Tips For Preventing Chimney Cracks
The maintenance condition of chimneys helps avoid both safety hazards and expensive repair costs. Executing these practices decreases the probability of chimney cracks developing.
Regular Maintenance
The prevention of cracks depends on regular maintenance which helps discover problems while they are still minor. The start of each year requires inspections to reveal potential small cracks or weather-related damage before their expansion becomes severe.
The accumulation of soot and debris needs to be cleaned annually because it causes damage to the lining which results in cracks forming.
The presence of water due to an absent or defective chimney cap results in rapid development of chimney cracks.
The inspection should focus on searching for architectural erosion marks such as gaps between bricks and mortar breakage or crack formation in masonry structures.
Hire CSIA-certified professionals for all maintenance work since they hold the needed expertise to maintain chimneys properly. Future structural evaluation requirements together with future large-scale repair costs will result from failing to maintain regularly scheduled care.
Using Quality Materials
The materials used for construction determine how long a chimney can last. The use of poor quality materials results in higher probabilities for developing cracks.
The selection of high-quality mortar for repointing during masonry work allows you to avoid damage from weather changes against masonry cracks.
The installation of suitable flue lining materials using stainless steel reduces chances of new cracks forming.
To block water from infiltrating into the structure homeowners should use waterproof sealants.
Quality material investments at the initial stage will prevent homeowners from performing multiple crack repair operations. Professionals should select materials and products made for United States weather zones that experience freeze-thaw cycle conditions.
Monitoring Weather Effects
Weather conditions act as strong contributors to chimney deterioration that occurs over time. Regular observation enables prevention of weather-related flaws.
Porous masonry allows moisture to seep in before ice expands inside and advances to create cracks. Keep brick sealed and protected.
Check your chimney exterior for all signs of visible damage and cracks after intense storms.
The sudden shift of heat causes structural strain which results in cracks.
Perform necessary checks to evaluate chimney stability after major weather occurrences. We suggest contacting the National Fire Protection Association (NFPA) because they provide reliable information about handling chimney problems which result from weather conditions.
Conclusion
Performing an inspection of chimney cracks enables people to verify durability alongside safety and operational efficiency. Thorough early issue identification leads to both affordable maintenance and defends our homes from potential water leaks together with fire dangers.
Masonry weakens over time due to the damaging effects of weather-induced cracks from freeze-thaw cycles along with storms. Storm inspections will discover early signs of trouble.
Measurements of small hairline cracks need special attention since they indicate potential issues beneath the surface. Well-trained experts utilize diagnostic equipment to expose concealed building damage.
A thorough analysis of crack depths helps experts decide what exact actions need to be taken to repair or maintain different structures.
Once cracks become evident professionals conduct specific repairs of both crack sealing and crack waterproofing to fix separate issues. Expert assessments during structural stability checks determine the integrity of chimneys to protect their safety alongside reliability.
As a result of inspections neglect the masonry cracks will evolve into drafts as well as smoke seepage which can grow into dangerous situations. To avoid making the problem worse always depend on certified professionals who perform chimney repairs. Obtain trusted guidelines by referring to materials at both the Chimney Safety Institute of America and the National Fire Protection Association.
Regular proactive maintenance of chimneys seeks to prevent unexpected water damage from dripping down the fireplace.
Frequently Asked Questions
What are the dangers of ignoring chimney cracks?
Ignoring chimney cracks can lead to structural damage, water leaks, smoke leaks, and increased fire risks. Small cracks may worsen over time, causing costly repairs and allowing harmful gases like carbon monoxide to seep into your home. Addressing cracks early ensures safety and efficiency.
How often should I inspect my chimney for cracks?
It’s recommended to inspect your chimney annually, especially before the heating season. Regular inspections help identify both visible and hidden damage early, preventing major issues and ensuring the chimney’s structural integrity.
What causes chimney cracks to form?
Chimney cracks are caused by factors like weather conditions (freeze-thaw cycles, heat), foundation settling, poor construction, and neglect. Regular maintenance and high-quality materials can help reduce the risk of cracking.
Can I repair chimney cracks myself?
Minor cracks can be addressed with sealants or patching, but professional evaluations are crucial to detect deeper issues. For significant damage, expert repairs like flue relining or chimney reconstruction may be necessary.
What are the signs that my chimney needs inspection?
Visible cracks, water leaks, drafting problems, or water stains near the fireplace are signs that your chimney requires inspection. These issues may indicate structural deterioration or airflow disruptions, demanding immediate attention.
How can I prevent chimney cracks?
To prevent chimney cracks, schedule annual inspections, clean regularly, use durable materials, and maintain chimney caps. Monitor for weather damage, especially after freeze-thaw cycles or storms, and address any issues promptly.
What tools do professionals use during chimney crack inspections?
Professionals use tools like chimney cameras, moisture meters, and specialized equipment to assess cracks, uncover hidden damage, and evaluate the chimney’s condition comprehensively.
Are chimney cracks always visible?
No, not all chimney cracks are visible to the naked eye. Hidden cracks can exist within flue liners, masonry, or other internal structures, which is why professional inspections are essential.
When is chimney reconstruction necessary?
Chimney reconstruction is required for severe damage, such as foundational cracks or extensive structural issues. This process restores structural stability and ensures safe operation.
Why is chimney maintenance so important?
Regular chimney maintenance protects your home from fire hazards, water damage, and carbon monoxide leaks. Proactive care ensures the chimney’s longevity, safety, and performance while reducing the need for costly repairs.